Material and Equipment Tracking Template
More electrical-construction templates
Ensure the timely availability of materials and equipment in your electrical construction projects with this comprehensive tracking template. This template helps managers monitor resource usage, set reorder points, and schedule maintenance to avoid delays and ensure efficient resource allocation.
By using this template, you can streamline your tracking processes, maintain up-to-date inventory records, and optimize your ordering and maintenance procedures, ultimately ensuring smooth project progress.
Get this template on priority matrix
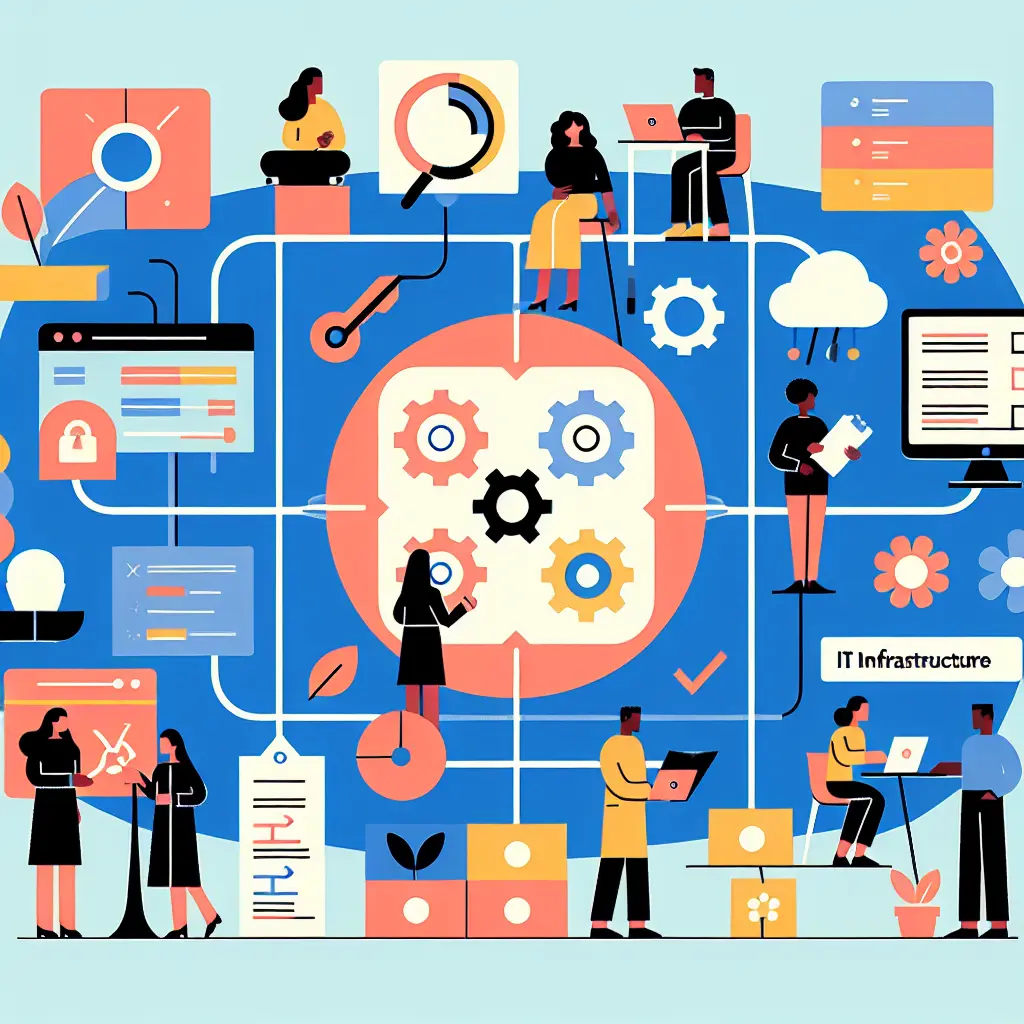
Material and Equipment Tracking in Priority Matrix
Monitor and manage the usage and availability of materials and equipment for efficient electrical construction projects.
You can start using Material and Equipment Tracking or other Electrical-Construction Project Templates with Priority Matrix in just a few steps:
- Click to sign in or create an account in the system
- Start adding your items to the matrix
- If you prefer to use the Mac and Windows app download Priority Matrix and take your data with you
Proposed Tasks
Critical and Immediate
-
Inventory Check - due in 1 day
☐ Check the current inventory of all materials and equipment ☐ Update the inventory list -
Equipment Usage Tracking - due in 1 week
☐ Track daily usage of equipment ☐ Update records -
Material Usage Tracking - due in 1 week
☐ Track daily usage of materials ☐ Update records -
Ordering Material - due in 6 weeks
☐ Order materials that are below reorder point ☐ Confirm delivery dates -
Equipment Maintenance - due in 7 weeks
☐ Perform scheduled maintenance on equipment ☐ Update maintenance records -
Inventory Check - due in 9 weeks
☐ Check the current inventory of all materials and equipment ☐ Update the inventory list -
Ordering Material - due in 10 weeks
☐ Order materials that are below reorder point ☐ Confirm delivery dates -
Equipment Maintenance - due in 11 weeks
☐ Perform scheduled maintenance on equipment ☐ Update maintenance records -
Inventory Check - due in 13 weeks
☐ Check the current inventory of all materials and equipment ☐ Update the inventory list -
Ordering Material - due in 14 weeks
☐ Order materials that are below reorder point ☐ Confirm delivery dates -
Equipment Maintenance - due in 15 weeks
☐ Perform scheduled maintenance on equipment ☐ Update maintenance records
Critical but not Immediate
-
Material Reorder Points - due in 2 weeks
☐ Set reorder points for each material ☐ Set up automatic reorder notifications -
Equipment Maintenance Schedule - due in 2 weeks
☐ Create maintenance schedule for each piece of equipment ☐ Set up maintenance notifications -
Equipment Usage Report - due in 8 weeks
☐ Prepare monthly equipment usage report ☐ Identify patterns and trends -
Material Usage Report - due in 8 weeks
☐ Prepare monthly material usage report ☐ Identify patterns and trends -
Equipment Usage Report - due in 12 weeks
☐ Prepare monthly equipment usage report ☐ Identify patterns and trends -
Material Usage Report - due in 12 weeks
☐ Prepare monthly material usage report ☐ Identify patterns and trends
Not Critical but Immediate
-
Supplier Contact Information - due in 3 weeks
☐ Update supplier contact information ☐ Set up communication channels with suppliers -
Ordering Process Optimization - due in 4 weeks
☐ Analyze current ordering process ☐ Suggest improvements ☐ Implement changes
Not Critical or Immediate
-
Staff Training on New Processes - due in 5 weeks
☐ Train staff on new ordering process ☐ Train staff on equipment maintenance process