Inventory Management and Replenishment Template
More operations templates
Maintain seamless production in the valve manufacturing industry by effectively managing inventory and replenishment processes. This template guides you through setting up an inventory tracking system, defining critical stock levels, and establishing reorder reminders to prevent stockouts.
With regular audits and staff training, this template ensures that your inventory management system remains accurate and efficient, minimizing disruptions in production due to supply shortages.
Get this template on priority matrix
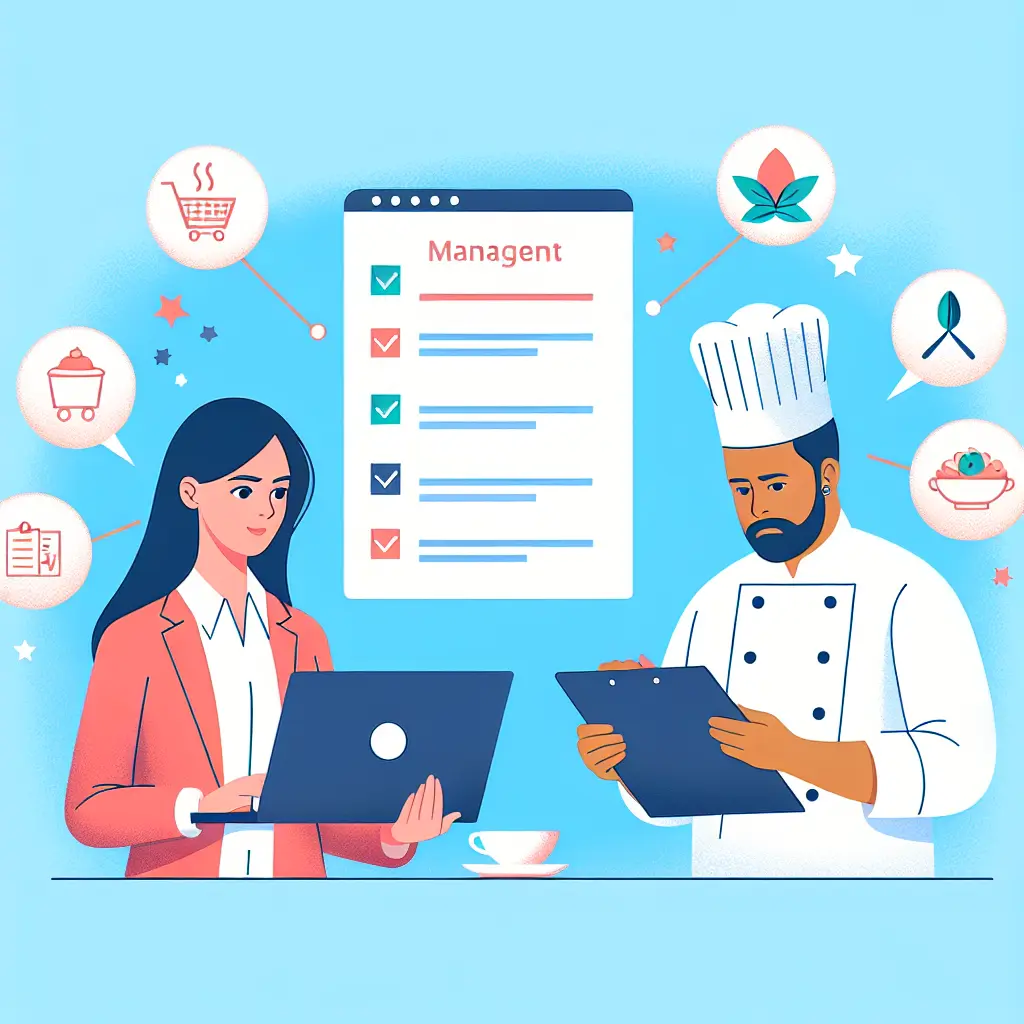
Inventory Management and Replenishment in Priority Matrix
Ensure continuous production by monitoring stock levels and setting up timely reorder processes in valve manufacturing.
You can start using Inventory Management and Replenishment or other Operations Project Templates with Priority Matrix in just a few steps:
- Click to sign in or create an account in the system
- Start adding your items to the matrix
- If you prefer to use the Mac and Windows app download Priority Matrix and take your data with you
Proposed Tasks
Critical Stock Levels
-
Task 2: Define critical stock levels - due in 2 weeks
☐ Determine the minimum stock levels for each valve type ☐ Set up alerts for when stock reaches these levels -
Task 7: Refine inventory levels - due in 8 weeks
☐ Adjust critical stock levels based on production needs and supplier lead times -
Task 12: Review critical stock levels - due in 18 weeks
☐ Review and adjust critical stock levels based on current production needs -
Task 17: Review critical stock levels - due in 28 weeks
☐ Review and adjust critical stock levels based on current production needs
Inventory Monitoring
-
Task 1: Set up inventory tracking system - due in 1 week
☐ Choose an inventory tracking system ☐ Configure the system to track valve stock ☐ Train staff on how to use the system -
Task 4: Test inventory system - due in 4 weeks
☐ Run a test of the inventory system to ensure it is working properly
Reordering Process
-
Task 3: Set up reorder reminders - due in 3 weeks
☐ Configure the inventory system to send reminders when stock reaches critical levels -
Task 5: Train staff on reordering process - due in 5 weeks
☐ Train staff on how to reorder stock when they receive a reminder -
Task 9: Review reorder process - due in 12 weeks
☐ Review the reorder process and make any necessary adjustments -
Task 10: Train staff on any system updates - due in 14 weeks
☐ Train staff on any updates to the inventory system or reorder process -
Task 14: Review reorder process - due in 22 weeks
☐ Review the reorder process and make any necessary adjustments -
Task 15: Train staff on any system updates - due in 24 weeks
☐ Train staff on any updates to the inventory system or reorder process -
Task 19: Review reorder process - due in 32 weeks
☐ Review the reorder process and make any necessary adjustments -
Task 20: Train staff on any system updates - due in 34 weeks
☐ Train staff on any updates to the inventory system or reorder process
Inventory Audits
-
Task 6: First inventory audit - due in 6 weeks
☐ Perform an inventory audit to ensure the system is tracking accurately -
Task 8: Second inventory audit - due in 10 weeks
☐ Perform a second inventory audit to ensure the system is still tracking accurately -
Task 11: Third inventory audit - due in 16 weeks
☐ Perform a third inventory audit to ensure the system is still tracking accurately -
Task 13: Fourth inventory audit - due in 20 weeks
☐ Perform a fourth inventory audit to ensure the system is still tracking accurately -
Task 16: Fifth inventory audit - due in 26 weeks
☐ Perform a fifth inventory audit to ensure the system is still tracking accurately -
Task 18: Sixth inventory audit - due in 30 weeks
☐ Perform a sixth inventory audit to ensure the system is still tracking accurately