Inventory Management and Reordering Project Template
More medical-manufacturing templates
Maintain continuous production by monitoring inventory levels and ensuring an adequate supply of materials. This template guides you through identifying current inventory levels, setting reorder points, selecting and implementing inventory management software, and training staff.
Regular monitoring and reordering will prevent production delays and ensure a consistent supply chain for seamless operations.
Get this template on priority matrix
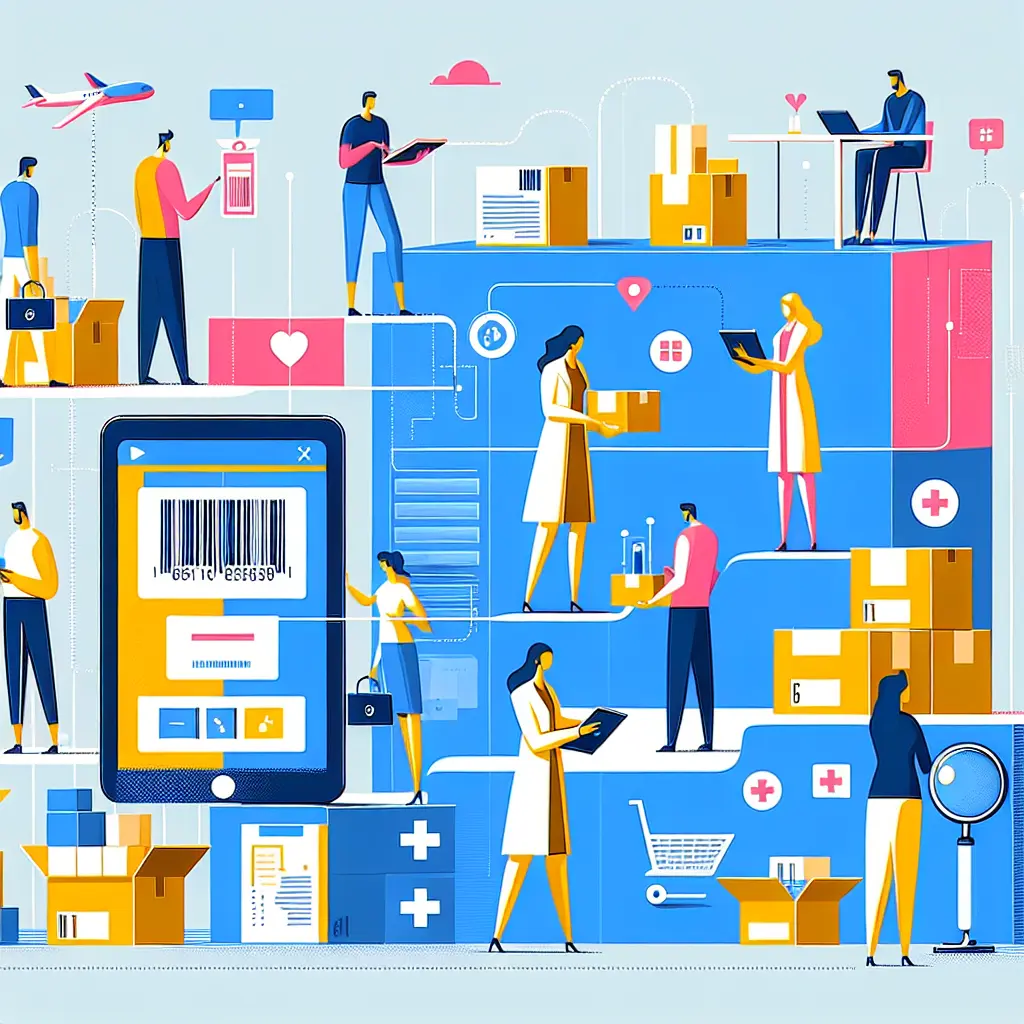
Inventory Management and Reordering Project in Priority Matrix
Ensure seamless production with effective inventory management and timely reordering.
You can start using Inventory Management and Reordering Project or other Medical-Manufacturing Project Templates with Priority Matrix in just a few steps:
- Click to sign in or create an account in the system
- Start adding your items to the matrix
- If you prefer to use the Mac and Windows app download Priority Matrix and take your data with you
Proposed Tasks
High Impact, Quick Wins
-
Task 1: Identify current inventory levels - due in 1 week
☐ Conduct a physical inventory count ☐ Document the results -
Task 2: Determine reorder points - due in 1 week
☐ Analyze past usage rates ☐ Calculate safety stock ☐ Set reorder points -
Task 3: Choose inventory management software - due in 2 weeks
☐ Research software options ☐ Compare features and costs ☐ Select the best fit -
Task 4: Train staff on inventory management software - due in 3 weeks
☐ Organize training sessions ☐ Ensure all relevant staff attend
High Impact, Long Term
-
Task 6: Monitor inventory levels - ongoing
☐ Check software for low stock alerts ☐ Conduct regular physical inventory counts -
Task 7: Place orders when stock reaches reorder point - ongoing
☐ Monitor inventory levels ☐ Place orders with suppliers when necessary -
Task 5: Implement inventory management software - due in 4 weeks
☐ Install software ☐ Input current inventory levels ☐ Test the software
Low Impact, Quick Wins
-
Task 8: Receive and check deliveries - ongoing
☐ Check deliveries against purchase orders ☐ Update inventory levels in software -
Task 9: Conduct regular inventory audits - every 3 months
☐ Plan audit schedule ☐ Conduct audits ☐ Compare results with software data
Low Priority / Etc.
-
Task 10: Review and adjust reorder points - every 6 months
☐ Analyze usage rates ☐ Adjust reorder points if necessary