Inventory Management and Tracking Template
More operations templates
Maintain an accurate and efficient inventory system for your Electric, HVAC, and Plumbing business. This template guides you through assessing current practices, researching and selecting an inventory management system, and implementing it effectively.
Improve operational efficiency by keeping track of tools, materials, and equipment, ensuring they are always available when needed, and avoiding delays due to lack of resources.
Get this template on priority matrix
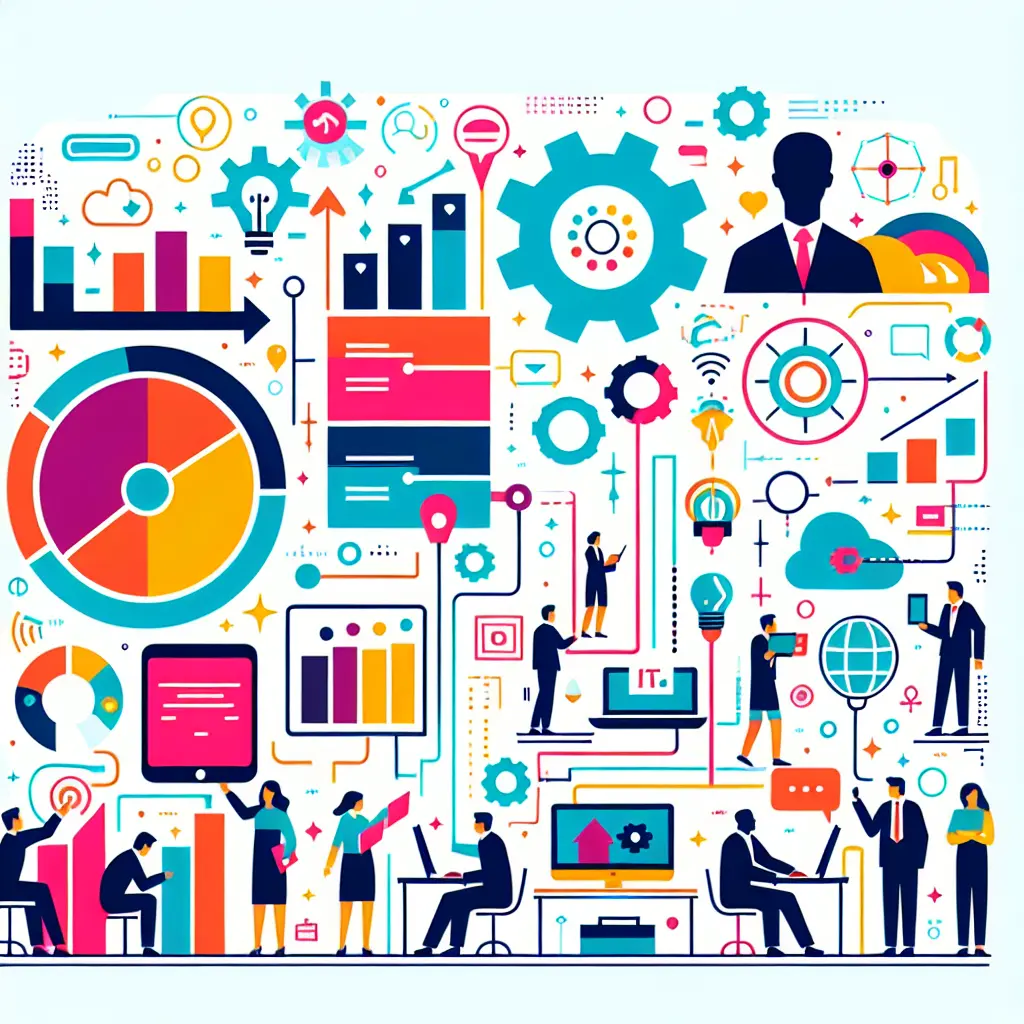
Inventory Management and Tracking in Priority Matrix
Ensure tools, materials, and equipment are always available with efficient inventory management and tracking.
You can start using Inventory Management and Tracking or other Operations Project Templates with Priority Matrix in just a few steps:
- Click to sign in or create an account in the system
- Start adding your items to the matrix
- If you prefer to use the Mac and Windows app download Priority Matrix and take your data with you
Proposed Tasks
Urgent and Important
-
Assess Current Inventory Practices - Due in 1 week
☐ Understand current inventory management methods ☐ Identify gaps and inefficiencies ☐ Document findings for future reference -
Select Inventory Management System - Due in 3 weeks
☐ Finalize the selection of the inventory management system ☐ Consider factors such as cost, ease of use, scalability, etc. -
Implement Inventory Management System - Due in 5 weeks
☐ Install and set up the selected inventory management system ☐ Input the prepared inventory database -
Train Staff on New System - Due in 6 weeks
☐ Conduct training sessions for staff on how to use the new system ☐ Ensure everyone understands the importance of accurate inventory tracking -
Review and Adjust System - Due in 3 months
☐ Review the effectiveness of the inventory management system ☐ Make necessary adjustments or improvements
Important, Not Urgent
-
Research Inventory Management Systems - Due in 2 weeks
☐ Explore different inventory management systems ☐ Compare features and prices ☐ Identify potential systems for implementation -
Prepare Inventory Database - Due in 1 month
☐ Create a comprehensive list of all tools, materials, and equipment ☐ Organize the list in a structured format for easy input into the system -
Regular Inventory Checks - Due in 10 weeks
☐ Establish a schedule for regular physical inventory checks ☐ Compare physical inventory with system records for accuracy -
Plan for Future Inventory Needs - Due in 4 months
☐ Forecast future inventory needs based on past usage and business growth ☐ Ensure the system can accommodate these needs
Urgent, Not Important
-
Monitor System Usage - Due in 8 weeks
☐ Regularly check the system to ensure it is being used properly ☐ Address any issues or concerns that arise